¿Qué es pickear productos? Picking o Preparación de Pedidos
¿Qué es pickear productos? ¿Qué es Picking?
Hay una pregunta que me han hecho en diversas ocasiones, sobre todo cuando la empresa decide contratar personal sin experiencia para las operaciones en bodega: ¿Qué es picking? ¿Qué es pickear productos?
Picking es un anglicismo ampliamente utilizado en el ámbito de las operaciones de bodega y logística. Se refiere al proceso de selección y recolección de productos o materiales específicos de un área de almacenamiento para completar un pedido o satisfacer una demanda.
El término «picking» proviene del verbo en inglés «to pick«, que significa «seleccionar» o «escoger». En el contexto de las operaciones de bodega, el picking es una actividad fundamental que implica la identificación y extracción de los productos necesarios de los estantes, racks o ubicaciones de almacenamiento.
Como proceso controlado, el objetivo principal del picking es garantizar la precisión y la eficiencia en la preparación de pedidos.
Importancia del picking en logística
Un proceso de picking eficiente y bien organizado ayuda a minimizar errores, optimiza los tiempos de entrega, aumenta la productividad y cumple con las expectativas de los clientes. Por otro lado, un mal proceso de picking puede provocar faltantes y generar insatisfacción, lo que puede llevar a que los clientes escriban reseñas negativas. Estas reseñas, a su vez, pueden influir en otros compradores y aumentar la tasa de abandono de carritos de compra.
Además, el picking juega un papel fundamental en la reducción de costos operativos y logísticos, ya que una ejecución eficiente del proceso minimiza los tiempos de inactividad, maximiza la capacidad de la bodega y optimiza la utilización de los recursos disponibles.
Un adecuado sistema de picking también permite una mejor gestión del inventario, ya que se puede realizar un seguimiento más preciso de los productos en stock y evitar situaciones de desabastecimiento o exceso de inventario.
Esto ayuda a optimizar la planificación y la gestión de la cadena de suministro, mejorando la toma de decisiones en cuanto a compras, reabastecimiento y distribución. Además, el picking eficiente tiene un impacto directo en la satisfacción del cliente.
Un proceso de recolección de productos ágil y preciso garantiza que los pedidos sean entregados en el tiempo prometido, con los productos correctos y en las cantidades requeridas [ Ver también: Logística de última milla y satisfacción del cliente ].
Esto ayuda a construir una reputación sólida y a generar lealtad por parte de los clientes, lo que se traduce en una mayor retención y en una ventaja competitiva en el mercado.
El proceso de picking se adapta a diversos métodos y estrategias que dependen de la naturaleza de los productos, el volumen de pedidos y la configuración de la bodega.
Existen almacenes y grandes centros de distribución que disponen de estructuras mecánicas automatizadas para las labores de picking, pero no me voy a centrar en ellas ahora, sino en las bodegas convencionales; aquellas que, aunque puedan tener dimensiones considerables, no cuentan con dichas estructuras automatizadas, y el trabajo es realizado por equipos de operarios o personal de bodega mediante el uso de montacargas o grúas horquilla.
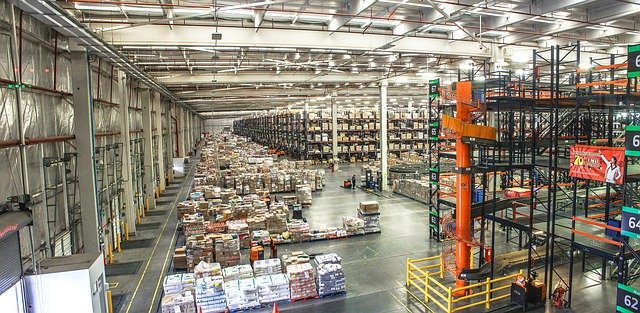
Etapas en el proceso de picking
El proceso de picking implica distintos momentos y actividades. Básicamente son las mismas para todo tipo de almacén, pero pueden variar según su tamaño y complejidad, así como los sistemas y tecnologías utilizados:
1.- Recepción de la orden o pedido:
- En esta etapa, se recibe la orden de recolección junto con los detalles del pedido, como los productos solicitados, las cantidades y la ubicación de almacenamiento. Esta información se registra en el sistema de gestión de almacenes.
2.- Pickear productos, seleccionar o recolectar:
- Los operarios se desplazan por el almacén para recolectar los productos de los distintos espacios de almacenamiento.
- Pueden utilizar métodos manuales o equipos de asistencia (grúas o montacargas, alza pallets manual o transpaletas), dispositivos de escaneo o sistemas de recolección por voz.
3.- Revisión y comprobación:
- Es importante realizar una verificación precisa durante el proceso de recolección para asegurarse de que se están seleccionando los productos correctos. Esto se puede lograr mediante la comparación de códigos de barras, números de lote o descripciones de productos.
4.- Empaquetado y etiquetado:
- Después de recolectar los productos, se empaquetan y se etiquetan de acuerdo con los requisitos específicos del pedido.
- Esto incluye la selección del tipo de embalaje adecuado y la aplicación de etiquetas con información relevante, como el nombre y dirección del cliente, número de pedido y cualquier otra instrucción especial.
5.- Verificación final:
- Antes de finalizar el proceso de picking, es importante realizar una verificación final para asegurarse de que se han recolectado todos los productos requeridos y que están en condiciones adecuadas.
- Lo anterior implica una revisión exhaustiva de los productos empaquetados y etiquetados, así como una comparación con la lista de productos del pedido.
6.- Consolidación de pedidos:
- En algunos casos, especialmente en operaciones de alto volumen, se lleva a cabo la consolidación de pedidos. Esto implica agrupar múltiples pedidos individuales en uno o varios envíos, lo que ayuda a optimizar el proceso de envío y reducir los costos logísticos.
Una vez realizado el picking se procede entonces al…
Empaquetado o Packing de productos
El packing es otro anglicismo de uso común en almacén y logística, y no es más que el empaquetado de los productos, la preparación adecuada para el transporte o envío a los distintos puntos de venta, o directamente al cliente final, cumpliendo así con la última etapa de una cadena de suministro y atendiendo a las buenas prácticas recomendadas en la denominada logística de última milla.
El proceso de empacado implica una serie de tareas que garantizan que los productos estén protegidos de manera adecuada y que el embalaje sea seguro y funcional. Estas tareas incluyen:
1.- Selección del contenedor o embalaje adecuado:
Seleccionar el tipo de embalaje adecuado es fundamental para asegurar la protección y seguridad de los productos durante el transporte. Esto puede incluir:
- Cajas de cartón
- Bolsas de plástico
- Envoltorios de burbujas
- Sobres acolchados
- Otros tipos de envases según tamaño, forma y fragilidad de los productos
2.- Organización y disposición de los productos:
- Los productos deben ser organizados y dispuestos de manera ordenada dentro del embalaje. Esto implica asegurarse de que los productos encajen correctamente, evitando movimientos internos que puedan causar daños durante el transporte.
- Es importante utilizar materiales de relleno, como papel, espuma o burbujas, para asegurar una posición segura y estable de los productos.
3.- Etiquetado adecuado:
Cada paquete debe ser etiquetado de manera clara y precisa. Esto incluye agregar etiquetas de dirección con la información del destinatario y el remitente, así como cualquier otra etiqueta requerida por las condiciones de envío o indicaciones especiales relacionadas con el contenido del paquete, por ejemplo:
- Nombre del destinatario.
- Dirección completa
- Peso de la caja o bulto
- Numeración de la caja o bulto, indicando además el número de cajas o bultos que conforman un mismo pedido (Caja 1 de 2; Caja 2 de 3, etc.)
- Otros, a conveniencia de la empresa
4.- Protección adicional:
- Dependiendo de la naturaleza de los productos, puede ser necesario aplicar medidas adicionales de protección. Por ejemplo, si los productos son frágiles, sensibles a la temperatura o requieren una manipulación especial, se deben agregar capas adicionales de protección, como materiales acolchados, divisores o separadores.
5.- Sellado adecuado:
- Es fundamental asegurarse de que el embalaje esté sellado de manera segura y resistente. Esto se logra utilizando cintas adhesivas de calidad o cualquier otro método de sellado adecuado para el tipo de embalaje utilizado.
- El sellado adecuado garantiza que los productos estén protegidos de la humedad, el polvo y cualquier otra posible interferencia durante el transporte.
6.- Registro y documentación:
- Es importante mantener un registro y documentación adecuada de los productos empaquetados. Esto puede incluir listas de contenido, facturas, formularios de aduana y cualquier otro documento necesario para el transporte y seguimiento del paquete.
- Es importante destacar que el momento exacto en el que se realiza el embalaje puede variar según el flujo de trabajo y las operaciones específicas de cada empresa.
- En algunos casos, el embalaje se realiza de manera inmediata después del picking, mientras que en otros puede haber etapas adicionales, como el control de calidad o la revisión final, antes de que los productos sean empaquetados.
- Además, en situaciones en las que se ofrecen servicios de personalización o ensamblaje, el embalaje puede incluir la colocación de etiquetas personalizadas, la inserción de folletos promocionales o cualquier otro elemento adicional que requiera el pedido del cliente.
- Es importante que el proceso de embalaje sea llevado a cabo con precisión y eficiencia para garantizar la satisfacción del cliente y la calidad del servicio. Un paquete adecuado no solo protege los productos durante el transporte, sino que también proporciona una experiencia positiva al cliente al recibir un paquete bien presentado y en condiciones óptimas.
[En este post encontrarás más información: «¿Qué es Packaging? El embalaje y la identidad de marca»].
Optimización del proceso de pickear productos
Existen diversas estrategias y prácticas que se pueden implementar para optimizar el proceso de picking en un almacén. A continuación, te muestro algunas de las formas más efectivas de mejorar la eficiencia y la precisión del picking:
1.- Análisis y diseño del layout de la bodega:
- El término «layout» se refiere a la disposición o diseño físico del espacio del almacén, es decir, la forma en que organiza y estructura el espacio y en los elementos dentro de ese espacio, para optimizar la eficiencia y funcionalidad de las operaciones, incluyendo equipos, maquinaria, estaciones de trabajo, áreas de almacenamiento, pasillos, áreas de circulación y otros elementos relevantes.
- Realizar un análisis exhaustivo del diseño de la bodega y su disposición es fundamental para optimizar el proceso de picking. Esto implica identificar las áreas de alto flujo, organizar los productos de manera lógica y estratégica, y minimizar las distancias y el tiempo de desplazamiento de los operarios.
- Un diseño bien planificado puede reducir con los tiempos de pickear productos.
2.- Clasificación de productos:
- Agrupar los productos en categorías o clases similares puede facilitar el proceso de recolección.
- Almacenar los productos de alta rotación cerca de las áreas de picking y mantener una ubicación consistente para los productos populares reduce los tiempos de búsqueda y agiliza el proceso de recolección.
3.- Etiquetado y marcado claro:
- Asegurarse de que los productos estén etiquetados y marcados de manera clara y legible es esencial para una recolección precisa.
- Usar códigos de barras, etiquetas de identificación o códigos SKU y tecnologías de escaneo por radiofrecuencia puede acelerar el proceso de pickear productos y reducir los errores.
4.- Implementación de tecnología:
- La incorporación de tecnología en el proceso de picking puede mejorar significativamente la eficiencia.
- El uso de dispositivos móviles, como escáneres de códigos de barras o terminales portátiles, permite a los operadores acceder a información en tiempo real, actualizar el estado de los productos y registrar las actividades de picking de manera más rápida y precisa.
- Además, los sistemas de gestión de almacenes (WMS) ofrecen funcionalidades avanzadas, como rutas de picking optimizadas, amortización automática de tareas y seguimiento de inventario en tiempo real.
5.- Capacitación y desarrollo de habilidades:
- Brindar capacitación adecuada a los operarios de picking es esencial para mejorar su desempeño. Esto incluye proporcionar instrucciones claras sobre las mejores prácticas de pickear productos, enseñar técnicas de organización y clasificación de productos, y promover la precisión y la atención al detalle.
- Por otro lado, fomentar un ambiente de aprendizaje continuo y desarrollo de habilidades ayuda a mantener al personal motivado y comprometido con la mejora del proceso de picking.
6.- Monitoreo y análisis de datos:
- El seguimiento y análisis de datos relacionados con el proceso de pickear productos proporciona información valiosa para identificar áreas de mejora.
- Usar métricas como el tiempo de recolección, la precisión de la recolección y la productividad de los operarios permite detectar patrones, identificar cuellos de botella y tomar decisiones informadas para optimizar el proceso.
7.- Mejora continua y retroalimentación:
- Establecer un ciclo de mejora continua es fundamental para optimizar el proceso de pickear productos a largo plazo. Promover el intercambio de ideas y conocimientos entre los operarios es una práctica valiosa para obtener diferentes perspectivas y enfoques sobre el proceso de picking.
- Al fomentar la colaboración y el trabajo en equipo, se crea un ambiente propicio para compartir experiencias, técnicas eficientes y soluciones innovadoras.
- Esta colaboración entre los operarios puede conducir a la identificación de mejoras significativas en el proceso de recolección y al descubrimiento de nuevas formas de aumentar la productividad y reducir errores.
Además de la colaboración entre los operarios, recopilar sugerencias y opiniones de todo el equipo es esencial para identificar oportunidades de mejora. Los operarios pueden aportar ideas basadas en su experiencia diaria en el almacén, ya sea relacionadas con el diseño del layout, la organización de productos, la utilización de herramientas o cualquier otro aspecto del proceso de recolección.
¡Bien, llegaste al final! Gracias por leerme. ¡Te espero en otro post!
Contenido relacionado:
- Primer día de trabajo en almacén o bodega
- ¿Qué es SKU y cómo aplicarlo en tu negocio?
- Supply Chain o Cadena de Suministro
Buenos dias estimado:
Gracias por toda esta valiosa información, me ayudó mucho a entender el proceso de picking.
Saludoa